Electric valve positioner maintenance calibration procedure describes positioner, according to the structure of pneumatic valve positioners, electric valve positioner and the smart valve positioner, is the main control valve accessories, usually supporting the use of pneumatic control valve which receives regulator output signal, then its output signal to control the pneumatic control valve when the valve action, displacement of the valve stem and feedback by mechanical means to the valve positioner, valve position status to the host system via electrical signals.
Electric valve positioner maintenance adjustment process:
4.1.1 Contact person handwheel chemical P4 opening control valve to maintain system stability.
4.1.2 Positioning and removal of the first film between the output connector (only by hand wheel in a particular direction of travel restrictions, can not restrict travel in both directions), so as not to increase the output overhaul locator, causing P4 valve opening increases, so that the hand wheel not properly controlled, cause swings.
4.1.3 repair or replace the unit set Xia. Ensure electrical parts intact, the range should be adjusted with reference to the valve stroke effect. Zero adjustment screw is then adjusted to a minimum, which is to ensure good electrical contact portion after the positioner no output.
4.1.4 notify the control room output signal is adjusted to the current valve valve opening corresponding to the signal, and then connect the output connectors and wiring portion of the retainer and the membrane head. At this point slowly adjust the positioner zero knob, so that the output pressure is gradually increased, while the other hand slightly hard to stop wheel valve opening direction until the hand wheel has a relaxed feeling (ie, the hand wheel has a relaxed feeling ( That has left the hand wheel, the first film has been replaced by a hand wheel pressure), adjust the rotation is stopped, then to notify the control room computer operation, and then the hand wheel rotation to the free position. the last step is justified reason to do so to follow.
We have tried, after removal of the positioner output connection, by blocking the output connector, according to the positioner output pressure gauge to determine the valve-grid position, results of course will not work. The next notable feature locator: Get a opening signal, if the valve is not in place, the positioning output will continue to increase until the output pressure to push the valve or air pressure, this anti-versa. In fact, that is, by the action of a feedback mechanism in order to achieve a balance of forces, and ultimately ensure that the valve opening degree and the master control room operation valve position signal correspondence. Similarly, the valve does not move under the circumstances, to send a opening degree is increased (or decreased), the positioner output will increase air pressure (reduced or no output pressure) unless the signal changes with the feedback shift lever corresponding to the degree of opening, which is obviously difficult to operate. The correct way is: send the current valve opening corresponding signal by zero knob gradually increased from the minimum film head thrust eventually replace the hand wheel, the feedback signal and the input signal to achieve a balance in order to achieve from the handwheel unperturbed support automatic switching operation.
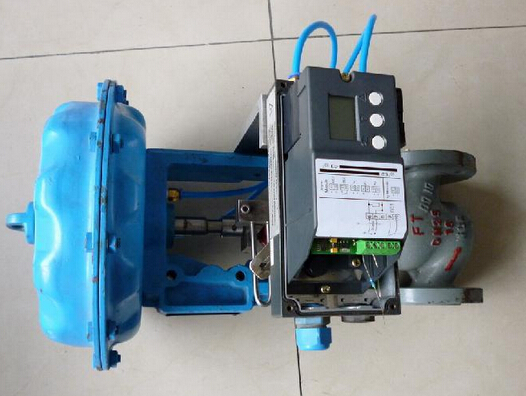
Positioner |